Author: Jason Sagorac, All-Lift Systems, Contrx Industries
Since the Industrial Revolution, overhead cranes have been put to use in a variety of diverse applications to move heavy and oversized objects that other material handling methods cannot. As your business changes with the introduction of new products or processes, so do your material handling requirements, and your existing overhead equipment may not be able to meet these demands. From the slow speeds and limited ratings of early cranes, we now find hoisting speeds of over 300 FPM, bridge speeds as high as 1,000 FPM, handling loads from 10 pounds to over 1,000 tons.
Three options exist for equipment improvement – buy a new crane, refurbish a used crane, or upgrade the present crane. All-Lift Systems, Contrx Industries works with today’s top providers such as Magnetek to provide & install solutions for up-grading your existing crane and demonstrate how today’s technology provides a cost-effective means to make your crane more efficient, productive, and safer. This article will discuss Control technology & AC Crane Modernizations.
Why Upgrade Or Modernize?
Increased production requirements may demand more capacity, faster operating speeds, better controls, or automation. Reliability may have deteriorated resulting in unscheduled shutdowns and increased production costs. Parts may be obsolete, resulting in high spare parts costs and long lead times. Inspections may show excessive wear or non-compliance with current safety standards or practices.
DC Crane Control Modernizations
Many find themselves today with aging overhead cranes, originally designed to perform and survive in the tough environments of steel and manufacturing plants but operating with the previous generation of high-maintenance DC motors and controls. There are some 3,000 active cranes running in North America with traditional DC controls that could be retrofitted over time.
Most of these older cranes rely on traditional electromechanical DC Constant Potential (DCCP) systems which use contactors to switch regenerative load currents to resistor banks in order to dissipate the energy. DCCP systems are maintenance intensive due to their many moving and wearing parts which must operate under severe duty and in harsh environments. Rather than scrap an outdated crane, which is still structurally and mechanically sound, it is more economical to upgrade or modernize these cranes with state-of-the art electronic controls, designed to meet current operational needs.
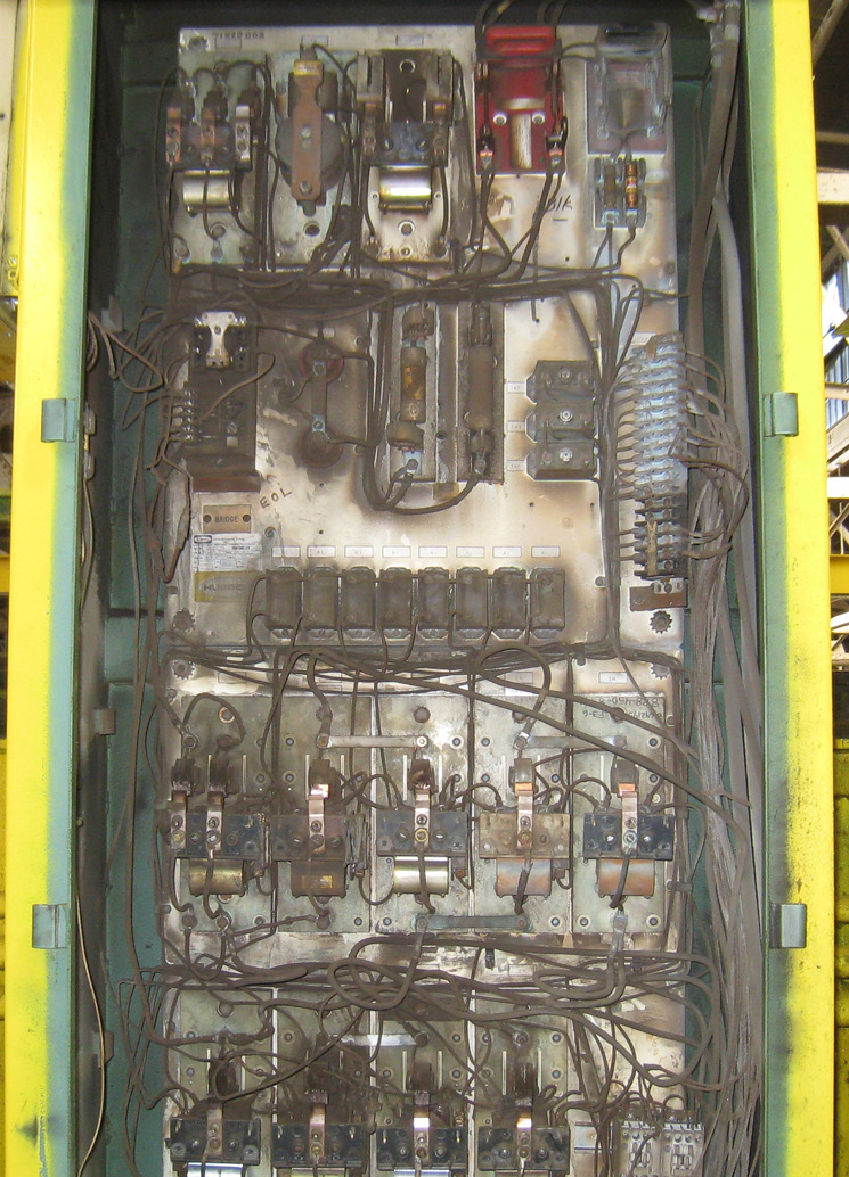
AC is becoming the power source of choice, especially for new installations in paper mills, steel mills, bulk materials handling, shipyards, and many more areas. However, DC motors are both efficient and robust and offer year upon year of service, providing acceptable performance for the most demanding applications. Retaining an existing DC motor and upgrading the crane with solid-state controls is more environmentally friendly and – from a commercial perspective – provides an opportunity to enhance overall system performance and reliability while minimizing the risk to production and the required capital investment, an attractive proposal in today’s economic environment. Three main control options are available for modernizing existing DC Cranes:
Retain existing power source, dc-motors and control wiring and replace traditional contactor control or obsolete static controls with Digital DC Controls.
- These microprocessor based, solid-state, four-quadrant DC-to-DC controls are designed for series, shunt, and compound wound motors and are a perfect drop-in replacement for traditional contactor control since they easily interface with existing power and control circuitry and use the same connection points while having a smaller footprint. This is the least costly option of the three, since existing motors, brakes, and wiring can often be utilized. In addition, energy savings can be significant, since these Digital DC Controls recover energy from the load and return it to the DC power supply.
Convert crane to operate on AC power retaining existing shunt-wound dc-motors and control wiring, replacing existing controls with DC Digital Static Drives.
- These drives are microprocessor digital logic controllers, which deliver precise, repeatable AC-in/DC-out control of shunt-wound bridge, trolley, and hoist motors -- with reliable, energy-efficient performance -- while significantly reducing operating and maintenance costs. This control has performance characteristics and many of the same advanced features of AC Adjustable Frequency Control. It can be an economical drop-in replacement for those cranes already equipped with shunt-wound dc-motors.
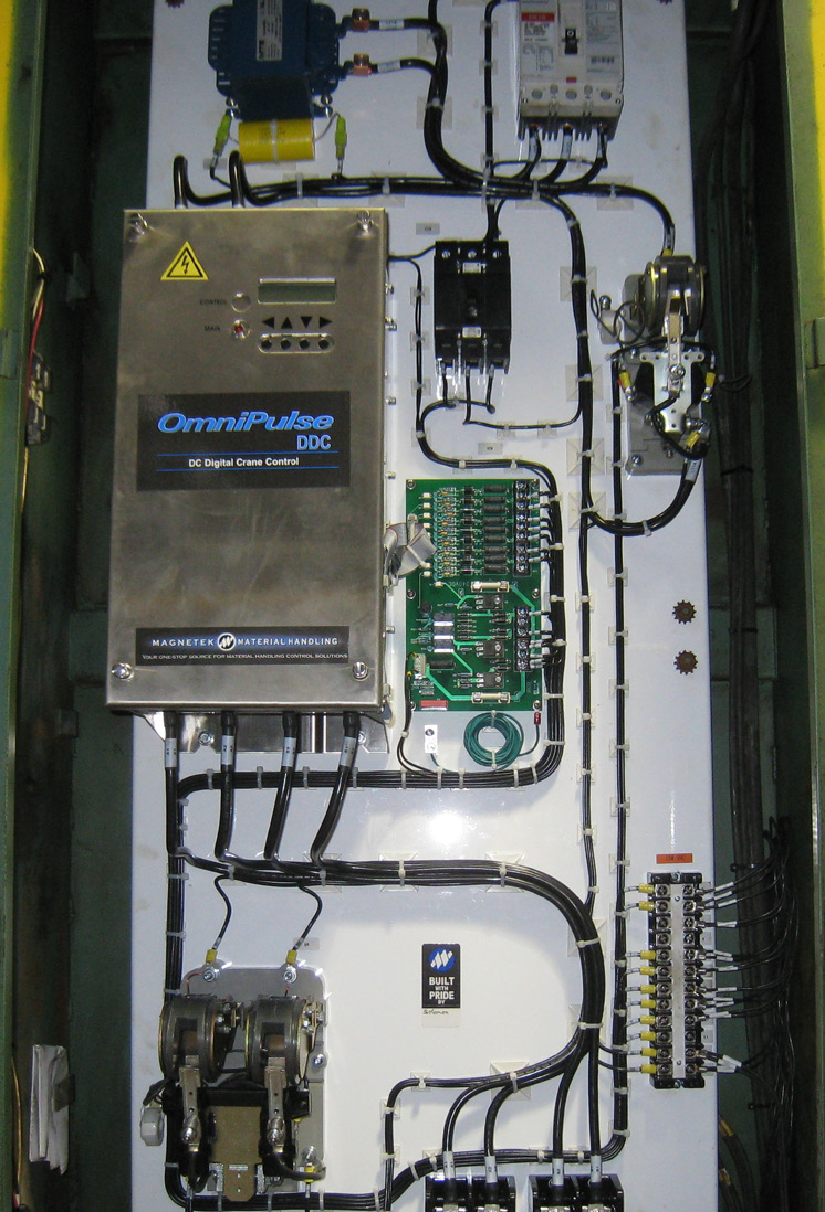
Convert crane to operate on AC power with low cost, efficient ac-motors andVariable Frequency Drives.
- Variable Frequency Drives have revolutionized the market for high performance AC Crane Controls -- now surpassing the torque control and speed regulation capabilities of DC shunt motor control.
Upgrading an aging DC crane with modern, robust and reliable DC or AC DigitalControls results in increased up-time, improved performance, reducedmaintenance costs plus energy savings, which all translate into a significantreturn on investment.
Conclusion
Overhead cranes represent a significant investment in capital. The MaterialHandling Institute (MHI) reports that “Companies spend billions of dollarsannually on material handling and logistics, representing anywhere from 20 to30% of their overall cost of doing business.” Therefore, rebuilding andmodernizing these assets with new modern parts and electric controls iseconomically prudent, since doing so protects and prolongs the life of theseinvestments, while saving as much as 30 to 40% of the cost of new equipment.
A crane modernization program may include capacity upgrades, new speed and motion controls, new brakes and other mechanical components, radio remote controls, independent traveling pendant pushbutton systems, cab-to-floor conversions, new festoon systems and mainline conductor systems, safety overload switches, warning devices, and anti-collision devices that adhere to all required safety standards.
Just a few years ago, cranes relied solely on contactors and static controls for their operation. Today, AC and DC drives are the preferred method of control -- but modern cranes utilize not only VFD technology but automation as well -- providing users with a wide variety of options to increase productivity, improve reliability and safety, enhance performance, and prolong equipment life, while affording many opportunities to increase profits and obtain a significant return on investment.
For more information on DC modernizations for your overhead crane, contact All-Lift Systems, Contrx Industries 800-236-2554 or sales@all-liftsystems.com and find out why it is All Lift, All The TIme!!